Étude de cas : Système de tri automatisé Modèle de simulation d'entrepôt
Contexte
Le client de SimWell est un détaillant en ligne de produits de grande consommation et d'autres produits d'épicerie. Il souhaite développer un modèle de simulation de système de tri automatisé pour une installation de traitement des commandes. Il souhaite déterminer les besoins en matériel pour un certain volume de commandes et le débit prévu. L'installation est toute neuve et l'objectif du modèle de simulation est de faciliter les choix de conception.
Objectifs
Les principaux objectifs du projet sont les suivants:
- Modéliser le réseau de convoyeurs et les postes de travail en fonction de la disposition.Rendre la disposition du modèle configurable en fonction des paramètres d'entrée. Le nombre de stations ainsi que le nombre de boucles de convoyeurs sont configurables.
- Déterminer le temps nécessaire pour chaque vague
- Déterminer l'utilisation des travailleurs et des postes de travail
- Optimisation du modèle pour:réduire le trafic sur le réseau de convoyeursréduire la distance de déplacement sur le réseau de convoyeurs
réduire le délai de traitement des commandes augmenter le débit - Développer une animation du modèle et un écran de démarrage configurable par l'utilisateur pour tester différents scénarios.
Résumé du processus
L'équipe de SimWell a développé un réseau de convoyeurs conforme à la configuration et pouvant être configuré en cas d'expansion ultérieure de l'installation en mettant à jour le nombre de boucles et de postes de travail dans le modèle. Tous les postes de travail ont été connectés en série à l'intérieur d'une boucle et toutes les boucles ont été reliées en série entre le convoyeur d'alimentation et le convoyeur de sortie. Les boucles sont reliées entre elles par des convoyeurs interconnectés. Les convoyeurs déplacent les caisses ou les cartons vers les postes de travail respectifs.
La simulation a été développée pour deux flux de processus différents avec deux modèles distincts, comme indiqué ci-dessous.
Livraison à la station
Il s'agit d'un processus d'exécution des commandes pour chaque poste de travail. Chaque poste de travail demande des commandes, et chaque commande comprend une variété de produits avec le nombre de quantités requises. La demande pour chaque poste est introduite dans le modèle par le biais d'une feuille Excel. Chaque caisse transporte une seule UGS (produit) en quantités variables. Les caisses transportant le SKU sont envoyées dans la station de travail pour fournir le nombre requis de quantités demandées par chaque commande. Si les caisses ne contiennent pas de quantités suffisantes, ces commandes restent en suspens jusqu'à ce qu'une caisse similaire réponde à leur demande. L'alimentation des caisses dans le réseau de convoyeurs se fera dans l'ordre séquentiel des données fournies sur la feuille d'entrée.
Les caisses sont poussées vers le réseau de convoyeurs avec les quantités d'UGS mentionnées dans Excel. Chaque caisse aura un numéro d'identification unique, un numéro d'identification de l'UGS et une quantité. Les caisses peuvent alimenter un ou plusieurs postes de travail en fonction de la demande. Une fois que les caisses ont été vidées à la station, elles peuvent être prélevées sur le réseau de convoyeurs de la station ou les caisses vides peuvent être autorisées à quitter le réseau au niveau du convoyeur de sortie. Le processus est synchronisé pour la livraison de chaque quantité de SKU.
Prise en charge à la station
Il s'agit d'un modèle inverse de celui de la livraison à la station. Chaque caisse est considérée comme une commande et est acheminée vide dans le réseau de convoyeurs. Les stations elles-mêmes disposent d'un stock de différentes UGS. Les caisses identifient la liste des postes de travail à atteindre à l'entrée de l'alimentation. Une logique a été développée pour envoyer le nombre limité de caisses à l'intérieur de chaque poste de travail. Si le poste de travail a été cartographié avec suffisamment de caisses et si une nouvelle caisse entrant dans le réseau contient ce poste de travail à atteindre en premier, cette caisse ne sera pas envoyée à ce poste de travail rempli. Au contraire, elle peut être déplacée vers le poste de travail suivant afin de faciliter le mouvement et de réduire l'attente et les délais. Chaque caisse peut prélever plusieurs UGS et une fois que toutes les UGS nécessaires ont été prélevées dans les stations respectives, la caisse se dirige vers le convoyeur de sortie pour quitter le réseau.
Regardez la vidéo du modèle ci-dessous:
En quoi la simulation a-t-elle été utile?
- La simulation avec animation du processus en 2D permet de déterminer la séquence optimale d'alimentation des caisses dans le système de convoyage,
- à réduire la file d'attente des caisses devant chaque poste de travail
- à choisir la configuration qui augmente le débit de l'installation.
- Il permet de déterminer le nombre de vagues pouvant être exécutées par jour.
- Le modèle peut être utilisé pour contrôler l'utilisation des postes de travail.
Scénarios
L'utilisateur peut simuler en modifiant certains paramètres contrôlables fournis sur l'écran de démarrage du modèle. L'utilisateur peut modifier les paramètres suivants:
- Type de convoyeur (de 3,5 m à 5,5 m de longueur de station)
- Vitesse d'alimentation par minute
- Espaces entre les caisses
- Taille des caisses
- Vitesse du convoyeur
- Seuil du temps d'attente dans la file d'attente
- Temps de traitement
- Nombre de niveaux dans les boucles
- Nombre de boucles
- Séquence d'alimentation des caisses
- Demandes des stations
Les résultats
Le modèle de simulation génère des résultats et des indicateurs clés de performance (KPI) importants énumérés dans la section des objectifs en fonction de différents scénarios et permet d'identifier la solution optimale.
Derniers articles publiés
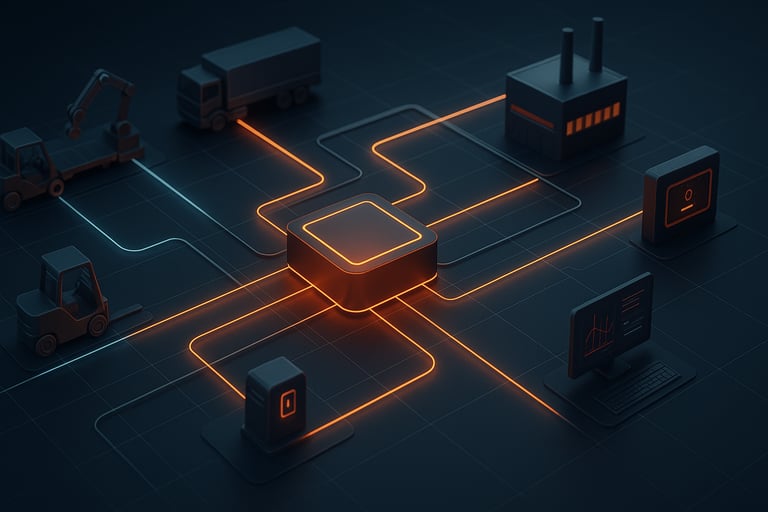
Ancrer la transformation numérique : comment les jumeaux numériques basés sur la simulation mettent l'accent sur le parcours
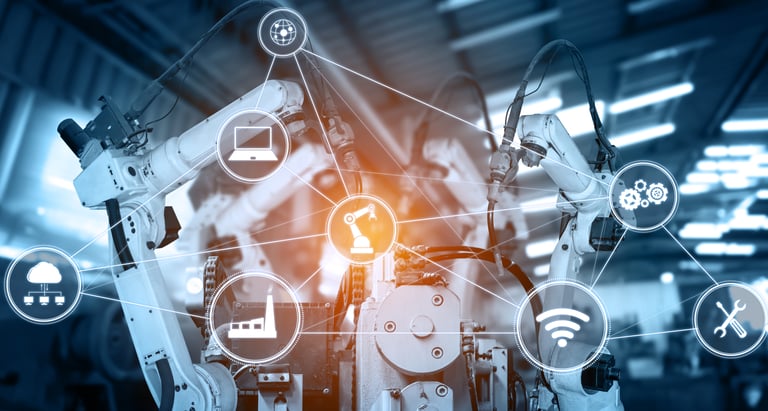
Repenser la stratégie d’entreposage à l’ère de la surabondance
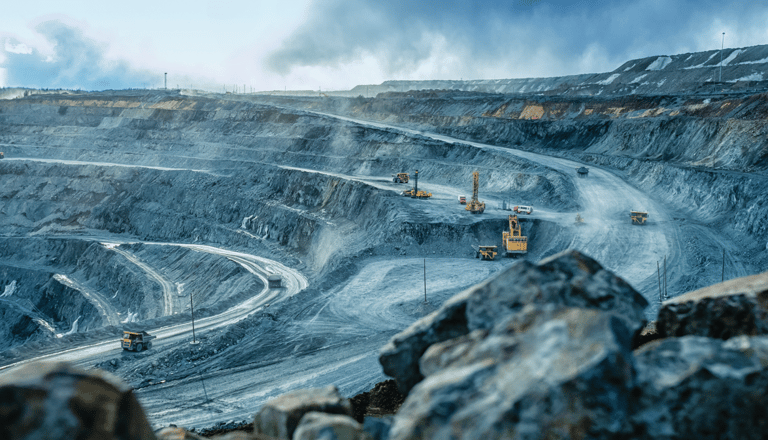