Case Study: How SimWell Helped a Beam Manufacturer Identify & Eliminate Bottlenecks
Overview
This project consisted of replicating the operations and finding the bottlenecks of a new beam manufacturing production line designed by the clients’ engineering team. The production line was partially based on experience from multiple parts of existing production lines. The model allowed for the easy manipulation of process parameters being tested against multiple scenarios. A follow-up meeting with the client indicated that the model was used extensively in the optimization of the production line to eliminate the bottlenecks. The model was also used to demonstrate the results to management in support of their decision-making process.
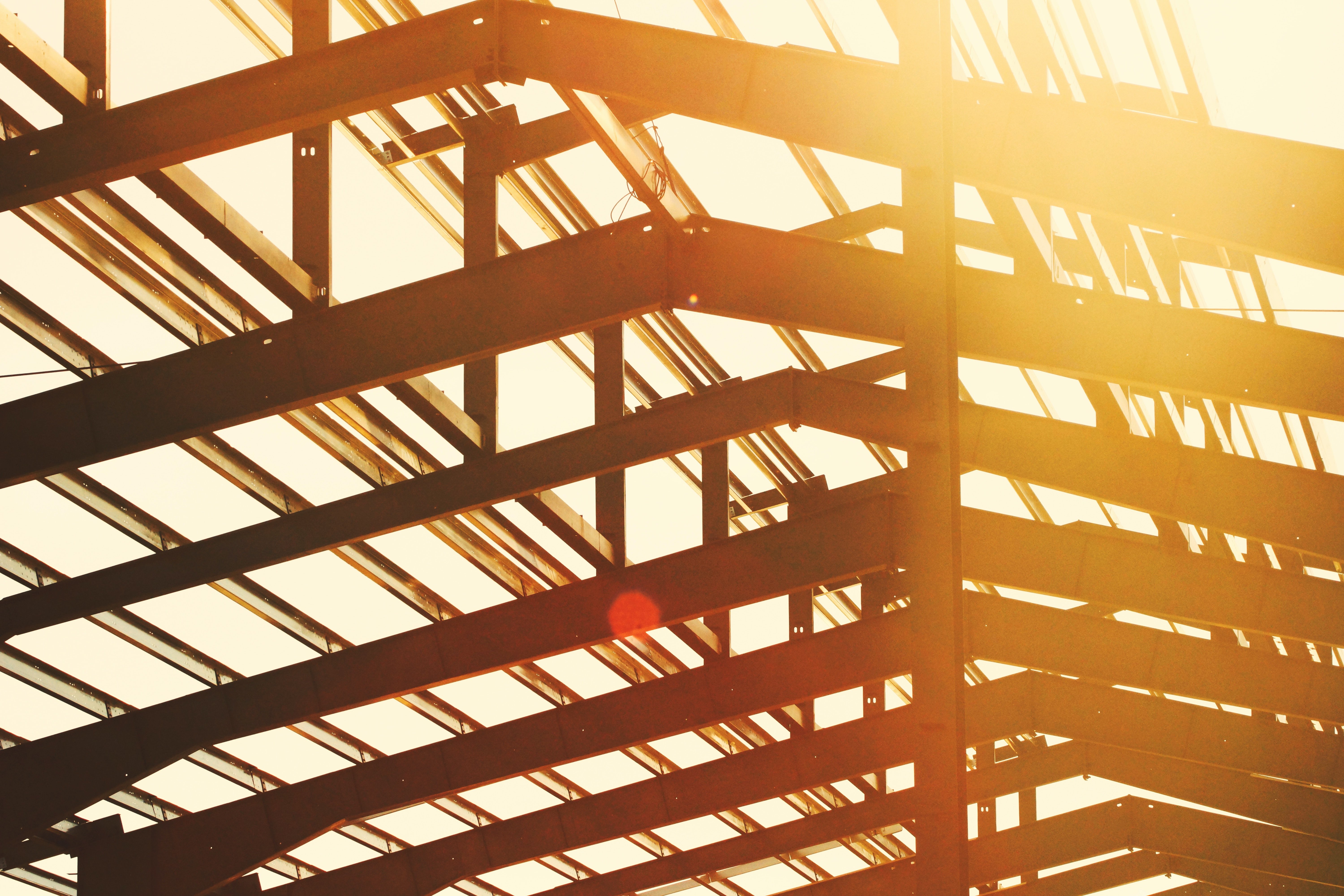
Background
The Beam Manufacturing Company is creating a new beam production line using a combination of process steps they are using at other beam production plants while also designing new process steps. The raw material utilized in the manufacturing process differs from that of other production facilities.
The Beam Manufacturing Company opted to use SimWell’s services for the design of a simulation model to study manufacturing bottlenecks and to present the production line and results to management.
The scope of the project starts when a forklift picks coils to load them on the machine and ends when the beam is produced by the production cell under study. The horizon of the simulation is 3 months of production.
Solution
SimWell developed a model of the beam manufacturing production line designed by the client. It was not possible to validate the model against real-life results since this is a new production line. As such, the model was presented to the client and approved as being a good representation of the beam manufacturing production line designed by the client’s engineering team.
The model was used to test a defined set of scenarios that included:
- Analysis of the impact of failures on the process
- Analysis of the historical operation sequencing
- Testing and analysis of different operations sequencing
- Assessment of the forklift utilization given certain parameters
- Use of 16 to 23 different types of coils
The model was evaluated in accordance with the following Key Performance Indicators:
- Beam production in feet/minute
- Resource utilization
- Number of times blocked
- Average time blocked
- Busy
- Idle
- Starving
The model accounts for the following parameter changes and variabilities:
- Production schedule (quantity and sequence)
- Production rate
- Setup time
- Cycle time
- MTBF / MTTR
- Support equipment (quantity and performance)
- Human resources (number, location, speed, etc.)
The Outcome
The tests and the feedback from the client demonstrate how important of a tool it is for them since it will enhance their supply operations and their global supply chain performance. The solution that SimWell built will serve as a decision-making tool for the client. Knowing the decision outcomes in advance will reduce a lot of supply chain costs. The tool allows the client to proactively test and choose the best policies for each one of their products in an extremely easy and fast way, thus ensuring better flexibility and service levels.