Case Study:
Trailblazing mining company partners with SimWell to optimize open-pit mining logistics
Summary
A mining company wanted to optimize their truck and shovel loading as well as hauling activities at their mining locations. They needed to examine truck interactions and behavior at intersections, giving priority based on multiple criteria. A fast and flexible simulation model was the best way to analyze multiple “what-if” scenarios quickly. Simwell created a simulation model that could draw different mining road networks based on input data, run simulations in under 30 seconds, and capture all the necessary data and KPIs in logs and dashboards.
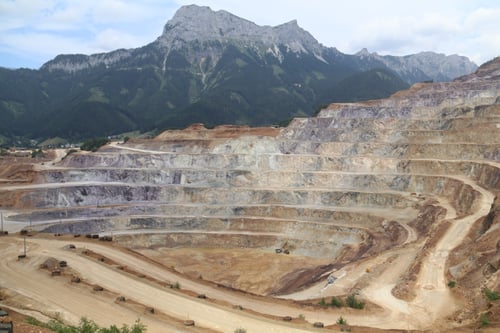
Challenge
One of the key challenges in open-pit mining logistics is ensuring that the trucks are loaded properly. This involves coordinating the loading process with the production process to ensure that the right amount of material is loaded onto each truck. Overloading or underloading can lead to safety issues or reduced productivity.
Another challenge is transportation routes that also need to be optimized to minimize travel time and distance. This requires the mapping of the mine’s geography and the location of the materials being transported. Route optimization can help reduce fuel costs, minimize wear and tear on the trucks, and reduce the environmental impact of the operation.
A trailblazing mining company is looking to overcome these challenges and improve the operational efficiency of their hauling fleets by examining current load & haul operations in many of their mines. To do this, they have reached out to SimWell, who determined that a simulation model would be the best tool to improve the day-to-day operations carried out by trucks and shovels.
Solution
-
The main goal of the project was to provide the capability to foresee the impact of these elements:
- Truck interactions on roads and intersections (priority, speed, safety distance)
- Truck assignment strategies on an open-pit mine truck-shovel system
- Truck maintenance plans
- Truck fleet size and number of shovels
- Etc.
The client required that the model be usable for multiple mine locations, with the possibility of adding new mines in the future. To achieve this, the simulation model was created so that drawing of the mine road network and connecting locations of interest would be done automatically based on a data file added by the client. This allows them to have the capability to scale and use the model in an unlimited amount of mining sites.
Within the simulation model itself, two general truck cycles were created to simulate the truck movements throughout the mine:
- The main load/haul cycle where mined materials are loaded onto a truck at the blast location by a shovel, and then sent to an unloading location based on the material type.
- The secondary cycle, the truck service cycle happens (if needed) once the truck completes the unloading and includes activities such as refueling, maintenance, repairs, breaks, and shift changes. Once the service cycle is completed, the truck returns to the main loading-unloading cycle.
Special attention was given to road intersections and truck interactions, allowing the user to modify the priority system of trucks at intersections. In addition, logic constraints were added to the road network for the speed and safety distance (among others) between trucks as indicated by the client.
The simulation model collects and presents several KPIs such as:
- Quantities of materials: Collected, transported, and delivered to each site based on quality.
- Distance traveled by each truck and types/quantities of materials it has carried.
- Queue times of trucks at shovels, dumping locations, and intersections.
- A record of every date/time, location, and type of cycle every truck carried out throughout the simulation.
- A record of every material type/quantity every shovel transferred to every truck.
Simulation results visualization was done in the form of a live dashboard where the user can quickly access important KPIs that they wish to see during the model run, as well as collecting all the simulation data in output files connected to an external dashboard and analytical tools of their choosing.
Results
The project's outcomes and benefits include increased safety, and productivity, reduced fuel costs, minimizing wear and tear on trucks and reduced environmental impact. The simulation model created by SimWell allows the client to set up different scenarios to optimize their truck fleet efficiency, test maintenance schedules, test different priority logics, and adjust the truck fleet size. By changing input data files and parameters, the model provides a visually representative representation of any mine, enabling the client to evaluate and optimize their mining operations. Overall, the developed solution enhances operational efficiency and allows the client to make informed decisions based on data-driven insights.