eCommerce Continues to Grow
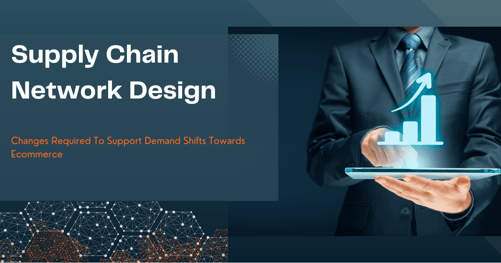
eCommerce amounted $3.82 billion USD in sales in December 2020 (according to Statistics Canada). Increasing demand for supply chain networks creates pressure so all companies are trying to deliver on time and at a reasonable cost. It is estimated that retail eCommerce will total US$40.3 billion in 2025.
The Question Everyone's Asking
How do I design my supply chain to meet demand within our service level expectations at the lowest cost? And how do I do that in the face of uncertainty, an increase in fuel costs, and rapid inflation?
The Answer
The answer is supply chain network optimization and simulation. eCommerce-first companies and traditional companies with a growing eCommerce segment manage complex supply chain operations. Spreadsheets and dashboards are great tools, but today's supply chains are comprised of complex, real-world problems with infinite variables, variability, and interactions that just do not fit on a spreadsheet.
That leaves leaders feeling utterly underwhelmed by the predictive tools at their disposal and overwhelmed by the massive decisions required to meet their growth, service, profitability, and sustainability goals.
Leaders need real answers based on the complexities of their operation.
The only way to capture the complexity of a supply chain is with network design tools that use optimization and simulation. Network design tools like anyLogistix accurately predict the outcome of decisions, preventing years of trial and error while also saving countless costs.
The tool provides a risk-free sandbox to model an operation, run dozens of scenarios, and compare the outputs of each so leaders can make confident, data-driven decisions that support their mission.
From Buzzwords to Practical Application
In our fast-paced world, we must embrace the continuous improvement of all supply chains.
There will always be changes in the network: new stores, new suppliers, and changes in costs. The optimal state of a supply chain network is ephemeral. As Peter Drucker said:
“If you can’t measure it, you can’t improve it.”
You don’t want to come up with an idea to improve something in the supply chain without knowing if it’s the real issue, right? More importantly, changes create riptides. The real supply chain network is not a good trial-and-error playground. It can get pricey—excessively pricey.
SimWell has developed myriad techniques to enhance the toolbox of supply chain experts, helping them achieve their objective to improve their supply chain continuously.
A Real-World Example
A retailer approached us with a fantastic riddle to solve. They were tasked to reduce delivery costs to customers while decreasing delivery times for online orders simultaneously.
Classic.
Now a bit of a background to set the table:
- One distribution center
- More than 25 stores across the country in 5 different provinces
- Thousands of products are delivered directly to customers through eCommerce
All products ordered online are sent from the distribution center. The distribution center sends 1-2 trucks weekly to each store. The retailer has an idea to use its store to fulfill online orders when possible.
But … which store? Should they all do it? Should they work together?
A Real Simulation Solution
With data on hand, we built a digital twin of their supply chain network with simulation software to test different “what-if’” scenarios. The first step is to create the base case, the virtual reality, where we ensure that costs are close to reality.
Now the fun begins! What if we use one store per province to fulfill online orders? What if we use each store as a delivery hub? What if we have one hub per province and all the other stores are satellites that can send it to the hub?
Obviously, many questions arose during the process:
- What happens if we don’t have the ordered product on-hand in the store?
- What if the online order took a product that would have been sold in-store?
- How many fewer orders will there be at the distribution center (DC)?
- How many trucks will depart from the DC with those changes?
- Are the stores big enough?
- What will be the peak inventory to face those online orders?
During working sessions, using the proven SimWell agile methodology, we have been able to gather as much information and data as required to help the retailer make the right decision. We have compared a few dozen scenarios to find the right balance between costs and service levels across online and in-store operations.
The Result
You must be asking yourself the important question: Was the riddle solved?
With a network design study, the client improved delivery time to customers for online orders by 50 percent and reduced total transportation costs by 5 percent while maintaining the same customer service level.
If your operations are expanding or changing, network design with SimWell will help you plan your business with confidence.
Connect with us. We'll reach out to you today.